Magnetron sputtering and cathodic arc ultra-high vacuum deposition system
This sample environment has been used for assessing the growth of coatings on a substrate, and deposition in multilayer neutron mirrors.
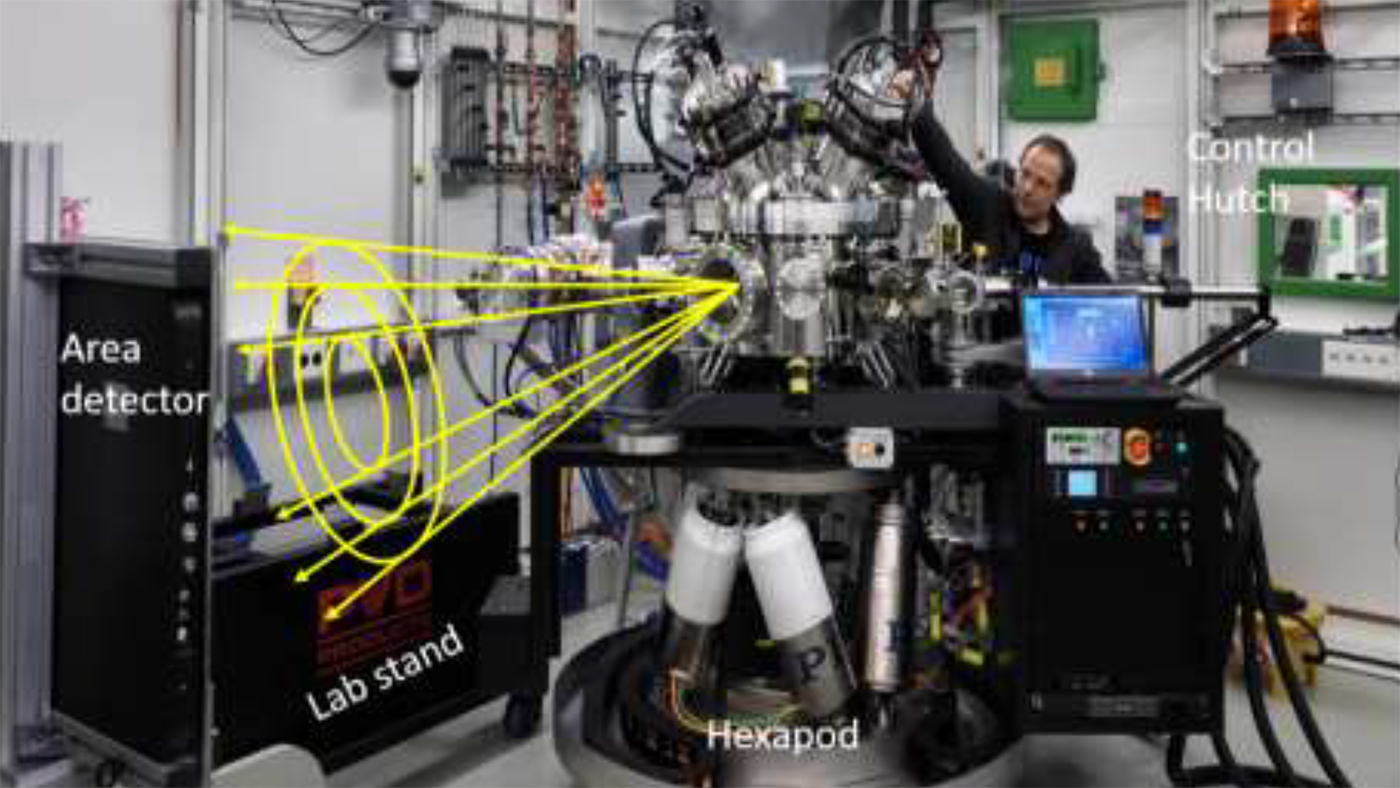
The deposition sample environment
The features of the magnetron sputtering and cathodic arc ultra-high vacuum deposition system are:
- Four 75 mm diameter DC UHV magnetron sputter sources
- Three 63 mm diameter UHV cathodic arc sources
- Base pressure <1 ⋅ 10−7 Pa (<1 ⋅ 10−9 Torr)
- Designed for use on 1-tonne ultra-high load hexapod for high-resolution sample alignment
- DC (100 V) and RF (125 W) substrate bias
- Laser-based susceptor heating >1400 °C with proportional-integral-derivative (PID) control via spectral band pyrometer
- Film/substrate temperature monitored via 2-colour pyrometer
- Chamber bake-out via internal heat lamps, heat blanket on control gate valve, and heat tape on the vacuum tee of the turbopumps
- Residual gas analyzer (XT100M; ExTorr) for both leak checking and monitoring gas composition during deposition processes
- Ports on chamber lid for kSA Multi-beam Optical Sensor (MOS) to perform real-time in situ monitoring of thin film stress
Thi is more fully described in J.L. Schroeder et al. (2015) Review of Scientific Instruments, Vol.86, No. 095113. doi.org/10.1063/1.4930243
Research examples using this sample environment
In their publication describing the sample environment, Schroeder et al. performed a demonstration measurement studying the growth of a Zr0.75Al0.25N coating on a Si substrate. The Si substrate was heated up to 700 °C and the deposition chamber pressure was set to 5 mTorr with an atmosphere of 10%N2/90%Ar, the background pressure before the introduction of the atmosphere gas was 2.0 × 10−9 Torr. A deposition rate of 20 nm/min was applied, using a Zr0.75Al0.25 target. Each SXRD image was acquired during a full 360° rotation of the sample. These measurements enabled observation of the thin film growth together with the characterisation of its crystalline structure.
Eriksson et al. used the same deposition system for the deposition of B4C-doped Ni/Ti multilayer neutron mirrors. The films were deposited on constantly rotating Si substrates. Depositions were performed without heating (even if available), at the ambient growth temperature. A 3 mTorr atmosphere of high purity Ar was set and 3 sputter sources were used in confocal geometry to realize the deposition. XRD in-situ measurement was performed, which enabled tracking of the crystallization of Ni and Ti over the deposition process, with and without B4C addition, revealing the efficiency of B4C to hinder crystallisation of Ni and Ti. This amorphization of the Ni/Ti multilayers is beneficial for the performance of the produced neutron mirrors.
For more information about this research case see: F. Eriksson, N. Ghafoor, D. Ostach, N. Schell, J. Birch, Ion-assisted magnetron sputter deposition of B4C-doped Ni/Ti multilayer mirrors, in: Advances in X-Ray/EUV Optics and Components XIII, SPIE, 2018: pp. 40–43. doi.org/10.1117/12.2317742
Both sets of experiments were performed at the P07 beamline at PETRA III. Due to the almost 1 tonne weight of this sample environment, the Roll-in station project needs to be completed in order to use this sample environment at the Swedish Materials Science beamline.